Elemental Upgrade - ElementDriven
ElementDriven, located in Vancouver WA, USA, makes aftermarket parts for 2003-2011 Honda Elements that enable owners to get the most out of their vehicles. The company was launched in early February 2021 to bring unique, new and innovative parts to the Element community.
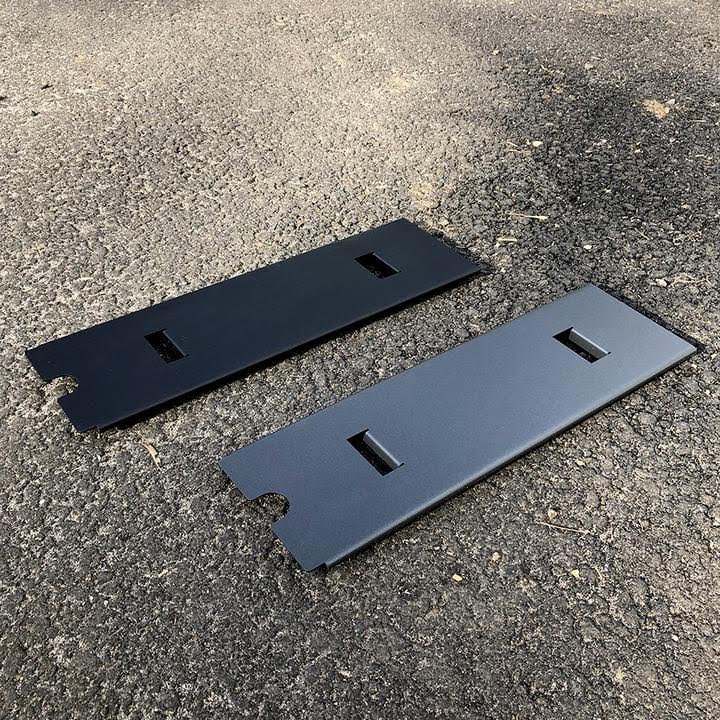
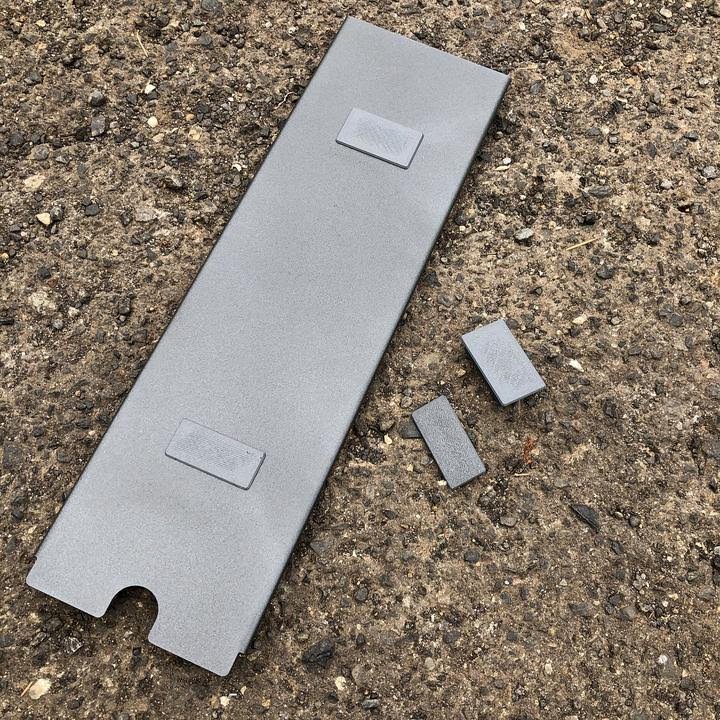
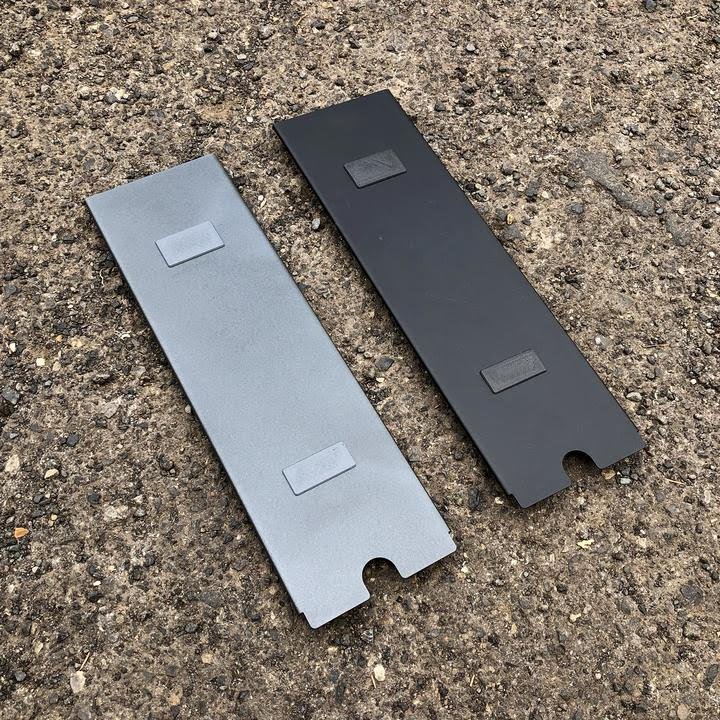
Rapid prototyping and scalable production
Jeff, the co-owner of ElementDriven, launched the company based on his Rear-Seat Floor-Latch Covers, a product that enables owners to get full use of their Element’s floor when they lift or remove their rear seats. Manufactured out of heavy-duty 16-gauge steel, they maximize the cargo space of the Element by securely leveling the floor to make it usable for transporting furniture, pets, kids, and more.
The floor latch covers had two openings from one-piece manufacturing of the tabs used to secure them to the Element’s floor, This meant there was a need to manufacture plugs to fill those openings to make this product safer and more functional. After weighing a variety of manufacturing options, Jeff decided to manufacture the plugs with FFF 3D printing for its great balance of functionality, cost-effectiveness, and adaptable parts particularly in low volume production runs.
Jeff reached out to Hydra Research in order to get the covers designed and manufactured quickly and affordably. Through our expertise, we were able to design a product that perfectly suited the application and the manufacturing technology. After discussing how the parts would be used, we determined that Nylon6 + GF30 by 3DXTech would be the best material for the job due to its excellent durability and added stiffness due to the glass fiber reinforcement.
“[Hydra Research] helped us get a product out that had been sitting idle for 6 months. [They] added a quality design change to our initial product idea which benefitted in providing a nice finished piece.”
Cost-effective parts for a niche market
Using Hydra Research’s 3D printing services ElementDriven was able to focus on their core products while leaving the design and production up to us. For small companies like ElementDriven, 3D printing allows for low-volume production of end-use parts at a price that would not be possible with traditional manufacturing methods. Without 3D printing and Hydra Research’s services, Jeff would have had much higher development and production costs for these plugs, which may have forced him to delay the part or abandon it entirely due to high cost. FFF 3D printing is a powerful process that allows companies like ElementDriven to service niche markets with products at reasonable prices that would have been challenging to do with traditional manufacturing.
Using Hydra Research’s 3D printing services ElementDriven was able to focus on their core products. Learn more about our 3D services and contact us to discover how you can save time and money using 3D printing for production.